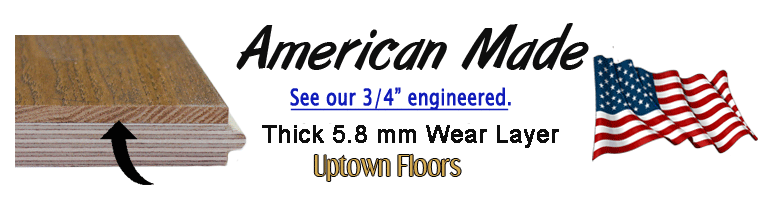
All times are UTC - 5 hours |
![]() ![]() |
Page 2 of 2 |
[ 30 posts ] | Go to page Previous 1, 2 |
|
Author | Message | |||||
---|---|---|---|---|---|---|
Ken Fisher |
|
|||||
Joined: Wed Aug 04, 2004 10:08 pm Posts: 1732 Location: Bonita Springs, Florida |
|
|||||
Top | |
|||||
![]() |
Floorguy |
|
||||
Joined: Thu Aug 05, 2004 5:44 am Posts: 3509 Location: Austin |
|
||||
Top | |
||||
![]() |
jfmoore75 |
|
||||
Joined: Wed Jun 08, 2005 6:38 pm Posts: 9 |
|
||||
Top | |
||||
![]() |
jfmoore75 |
|
||||
Joined: Wed Jun 08, 2005 6:38 pm Posts: 9 |
|
||||
Top | |
||||
![]() |
Ken Fisher |
|
|||||
Joined: Wed Aug 04, 2004 10:08 pm Posts: 1732 Location: Bonita Springs, Florida |
|
|||||
Top | |
|||||
![]() |
jfmoore75 |
|
||||
Joined: Wed Jun 08, 2005 6:38 pm Posts: 9 |
|
||||
Top | |
||||
![]() |
jfmoore75 |
|
||||
Joined: Wed Jun 08, 2005 6:38 pm Posts: 9 |
|
||||
Top | |
||||
![]() |
Floorguy |
|
||||
Joined: Thu Aug 05, 2004 5:44 am Posts: 3509 Location: Austin |
|
||||
Top | |
||||
![]() |
Gary |
|
||||
Joined: Sat Sep 25, 2004 7:42 pm Posts: 4373 Location: Antioch, CA. 94509 |
|
||||
Top | |
||||
![]() |
Ray Darrah |
|
||||
Joined: Thu Aug 19, 2004 6:02 pm Posts: 622 Location: Florida |
|
||||
Top | |
||||
![]() |
beachy*mama |
|
||||
Joined: Mon Aug 29, 2005 8:52 am Posts: 2 Location: SW Florida |
|
||||
Top | |
||||
![]() |
Ken Fisher |
|
|||||
Joined: Wed Aug 04, 2004 10:08 pm Posts: 1732 Location: Bonita Springs, Florida |
|
|||||
Top | |
|||||
![]() |
beachy*mama |
|
||||
Joined: Mon Aug 29, 2005 8:52 am Posts: 2 Location: SW Florida |
|
||||
Top | |
||||
![]() |
Floorguy |
|
||||
Joined: Thu Aug 05, 2004 5:44 am Posts: 3509 Location: Austin |
|
||||
Top | |
||||
![]() |
Serbonze |
|
||||
Joined: Tue Dec 21, 2004 11:04 am Posts: 63 Location: Tampa, FL |
|
||||
Top | |
||||
![]() |
![]() ![]() |
Page 2 of 2 |
[ 30 posts ] | Go to page Previous 1, 2 |
All times are UTC - 5 hours |
Who is online |
Users browsing this forum: No registered users and 0 guests |
You cannot post new topics in this forum You cannot reply to topics in this forum You cannot edit your posts in this forum You cannot delete your posts in this forum |