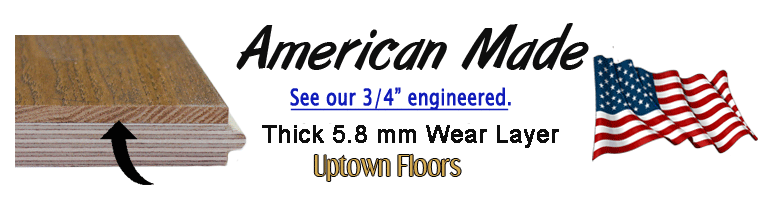
All times are UTC - 5 hours |
![]() ![]() |
Page 2 of 3 |
[ 38 posts ] | Go to page Previous 1, 2, 3 Next |
|
Author | Message | ||||
---|---|---|---|---|---|
Ray Darrah |
|
||||
Joined: Thu Aug 19, 2004 6:02 pm Posts: 622 Location: Florida |
|
||||
Top | |
||||
![]() |
dana |
|
||||
Joined: Fri Jun 08, 2007 8:52 pm Posts: 40 Location: CA |
|
||||
Top | |
||||
![]() |
Ray Darrah |
|
||||
Joined: Thu Aug 19, 2004 6:02 pm Posts: 622 Location: Florida |
|
||||
Top | |
||||
![]() |
Gary |
|
||||
Joined: Sat Sep 25, 2004 7:42 pm Posts: 4373 Location: Antioch, CA. 94509 |
|
||||
Top | |
||||
![]() |
Jerry Thomas |
|
||||
Joined: Tue Aug 17, 2004 1:26 am Posts: 1195 Location: Virginia |
|
||||
Top | |
||||
![]() |
dana |
|
||||
Joined: Fri Jun 08, 2007 8:52 pm Posts: 40 Location: CA |
|
||||
Top | |
||||
![]() |
dana |
|
||||
Joined: Fri Jun 08, 2007 8:52 pm Posts: 40 Location: CA |
|
||||
Top | |
||||
![]() |
Floorguy |
|
||||
Joined: Thu Aug 05, 2004 5:44 am Posts: 3509 Location: Austin |
|
||||
Top | |
||||
![]() |
Ray Darrah |
|
||||
Joined: Thu Aug 19, 2004 6:02 pm Posts: 622 Location: Florida |
|
||||
Top | |
||||
![]() |
dana |
|
||||
Joined: Fri Jun 08, 2007 8:52 pm Posts: 40 Location: CA |
|
||||
Top | |
||||
![]() |
Jerry Thomas |
|
||||
Joined: Tue Aug 17, 2004 1:26 am Posts: 1195 Location: Virginia |
|
||||
Top | |
||||
![]() |
dana |
|
||||
Joined: Fri Jun 08, 2007 8:52 pm Posts: 40 Location: CA |
|
||||
Top | |
||||
![]() |
Floorguy |
|
||||
Joined: Thu Aug 05, 2004 5:44 am Posts: 3509 Location: Austin |
|
||||
Top | |
||||
![]() |
dana |
|
||||
Joined: Fri Jun 08, 2007 8:52 pm Posts: 40 Location: CA |
|
||||
Top | |
||||
![]() |
Jerry Thomas |
|
||||
Joined: Tue Aug 17, 2004 1:26 am Posts: 1195 Location: Virginia |
|
||||
Top | |
||||
![]() |
![]() ![]() |
Page 2 of 3 |
[ 38 posts ] | Go to page Previous 1, 2, 3 Next |
All times are UTC - 5 hours |
Who is online |
Users browsing this forum: No registered users and 0 guests |
You cannot post new topics in this forum You cannot reply to topics in this forum You cannot edit your posts in this forum You cannot delete your posts in this forum |